2022.08.05
- 製造業
- ものづくり補助金
生産性向上に取り組む企業事例
切断・前処理・鍛造・切削・研磨などを一気通貫した部品製造 新たな機械導入でさらなる精度を実現【株式会社大和製作所】(長野県岡谷市)
自動車部品の製造で発展してきた大和製作所は、材料の歩留まりを良くし、顧客の期待に合わせられるよう、工程の工夫を積み重ねてきた。その1つが、冷間鍛造技術だ。熱を使わず常温で鍛造する技術で、熟練度が必要だが歩留まりが高く、ロスの少ないものづくりが可能となる。さらにその前後工程に関わる機械/装置を導入し、工程全体の生産性向上をめざす。
先進機械と一貫した生産体制で高いニーズに応える
エンジン用ギアシャフトやエアバッグ取り付け部品など、同社のつくる部品は自動車のさまざまな場所に使われている。1963年から導入している冷間鍛造技術は、材料ロスを出さずに短時間に多くの部品をつくるために欠かせない。自動車部品は、間違いのない製造と期日に合わせた確実な納入が求められる。
同社の強みは、切断・鍛造から二次加工まで一貫して対応できる点である。長年培ってきた金型製造技術で、精度の高い金型を内製できることも大きい。工程間の輸送の手間も削減でき、トータルコストも押さえられる。多様な製品ニーズに対応できるよう、冷間鍛造プレスの機械以外に、ナットフォーマー・パーツフォーマー、二次加工に必要な切削機械、ねじ転造機、研磨機械、検査に必要な各種測定器や検査装置などを多数揃える。
設備は徐々に整えてきたが、受注増加に伴い、さらに生産性を高められるところがないかと検討してきた。そのような折、ものづくり補助金が活用できることとなり、精密切削機械を新規導入することを決めた。冷間鍛造後の仕上げ工程で時間当たり対応できる量を拡大し、全体の生産性も高めたいと思ったからだ。
同社の強みは、切断・鍛造から二次加工まで一貫して対応できる点である。長年培ってきた金型製造技術で、精度の高い金型を内製できることも大きい。工程間の輸送の手間も削減でき、トータルコストも押さえられる。多様な製品ニーズに対応できるよう、冷間鍛造プレスの機械以外に、ナットフォーマー・パーツフォーマー、二次加工に必要な切削機械、ねじ転造機、研磨機械、検査に必要な各種測定器や検査装置などを多数揃える。
設備は徐々に整えてきたが、受注増加に伴い、さらに生産性を高められるところがないかと検討してきた。そのような折、ものづくり補助金が活用できることとなり、精密切削機械を新規導入することを決めた。冷間鍛造後の仕上げ工程で時間当たり対応できる量を拡大し、全体の生産性も高めたいと思ったからだ。
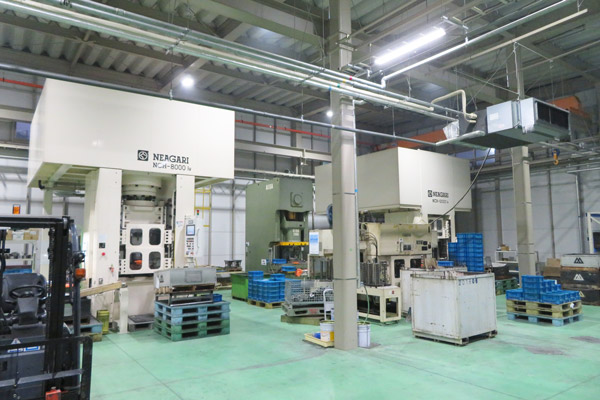
新たな機械の導入で、これまで出し得なかったスペックを実現
フォーマーや冷間鍛造プレスを使った塑性加工は、一部ではまだ粗い状態にある。刀をつくったあと研いで精度をあげていくように、塑性加工の部品もミクロサイズで合わせていくには、切削や研磨仕上げが重要となる。ミクロに合わせていくところに時間がかかっていたが、今回導入した機械では自動補正なども可能で、余計な調整の手間なく正確な仕上げをしていける。導入後はフル稼働している状態だ。
冷間鍛造だけでは出し得ないスペック、切削機械だけでは出し得ないスペックというものがあるが、新たな機械はこうした工程の組み合わせによる精度向上に大きく役立つ。さらに、時間生産性も高まった。作業工程を組み合わせるときに、ある工程は非常に効率よく進むが、ある工程では非常に時間がかかるといった差異があると、結局遅いネック工程に合わせた生産量にとどまってしまう。機械により生産性が改善できるならば、積極的に使いたいという考えもあった。
また、今回導入した機械は制御の安定性が高く、人が付きっきりにならなくても作業が進む。限られた人数で高い生産性を出していくには、こうした利便性の高さも重要だ。機械でおこなえる部分はできるだけ機械に任せ、それを最大限使いこなしていくことが重要だという考えにたつ。従業員は一定期間で適宜ローテーションしており、複数の工程を担当できる人が多い。前後の工程を知っていることで、作業効率や全体最適意識も高まる。
冷間鍛造だけでは出し得ないスペック、切削機械だけでは出し得ないスペックというものがあるが、新たな機械はこうした工程の組み合わせによる精度向上に大きく役立つ。さらに、時間生産性も高まった。作業工程を組み合わせるときに、ある工程は非常に効率よく進むが、ある工程では非常に時間がかかるといった差異があると、結局遅いネック工程に合わせた生産量にとどまってしまう。機械により生産性が改善できるならば、積極的に使いたいという考えもあった。
また、今回導入した機械は制御の安定性が高く、人が付きっきりにならなくても作業が進む。限られた人数で高い生産性を出していくには、こうした利便性の高さも重要だ。機械でおこなえる部分はできるだけ機械に任せ、それを最大限使いこなしていくことが重要だという考えにたつ。従業員は一定期間で適宜ローテーションしており、複数の工程を担当できる人が多い。前後の工程を知っていることで、作業効率や全体最適意識も高まる。
グローバルな変化を見据えつつ、柔軟性を持って対応できる力を高める
自動車関連の部品と言っても、いわゆる乗用車だけに使われているわけではない。たとえばトラクターなどの農業機械にも同社の部品が使われている。日本は人口減が進むが、世界を見ると人口増が進む地域も多い。すると食料生産の増加が喫緊の課題となり、アフリカなどの新興国ではこれから農業機械を導入し、大型農業をしていくことの広がりも予想される。
より広大な土地で、舗装もされていない道を走るような農業機械はグローバルで今後ますます求められていくことだろう。そうしたところで使われ続けるために、精度も高く、壊れない部品であることの重要性は高い。農業機械への部品供給はまだまだ拡大の余地があると考えているそうだ。ただ強度をあげるだけではなく、耐摩耗性をあげるなど、多様な工夫を組み合わせる。
同社の取引先である自動車業界は、EV化をはじめとする大きな変革の波がきている。ガソリン車に比べてEV車は部品点数も少なくなると言われる昨今だ。そうした変化はもちろん捉えつつも、だからといって考えることが大きく変わるわけではないという。さまざまな製品のなかに、多様な部品が使われている。どういった相談が来ても対応できるよう、現場力向上に力を入れ続けている。
より広大な土地で、舗装もされていない道を走るような農業機械はグローバルで今後ますます求められていくことだろう。そうしたところで使われ続けるために、精度も高く、壊れない部品であることの重要性は高い。農業機械への部品供給はまだまだ拡大の余地があると考えているそうだ。ただ強度をあげるだけではなく、耐摩耗性をあげるなど、多様な工夫を組み合わせる。
同社の取引先である自動車業界は、EV化をはじめとする大きな変革の波がきている。ガソリン車に比べてEV車は部品点数も少なくなると言われる昨今だ。そうした変化はもちろん捉えつつも、だからといって考えることが大きく変わるわけではないという。さまざまな製品のなかに、多様な部品が使われている。どういった相談が来ても対応できるよう、現場力向上に力を入れ続けている。
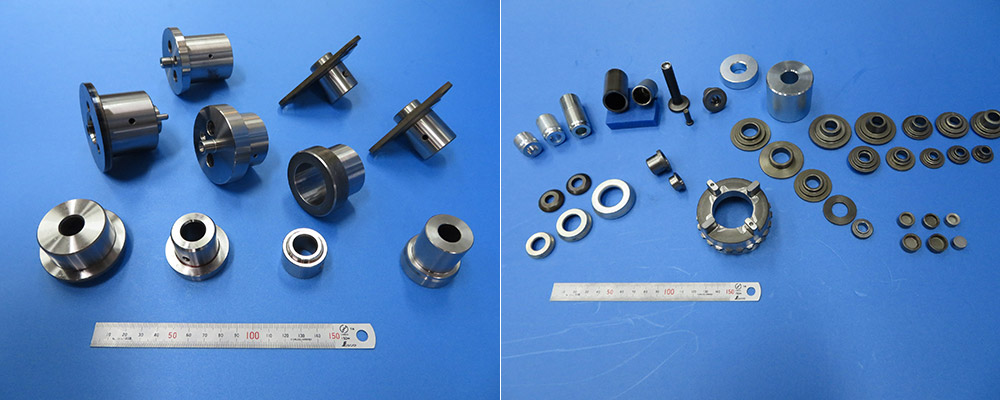
企業データ
- 企業名
- 株式会社大和製作所
- 設立
- 1945年
- 従業員数
- 110人
- 代表者
- 代表取締役社長 片倉 克昭 氏
- 所在地
- 長野県岡谷市川岸上1丁目2番1号